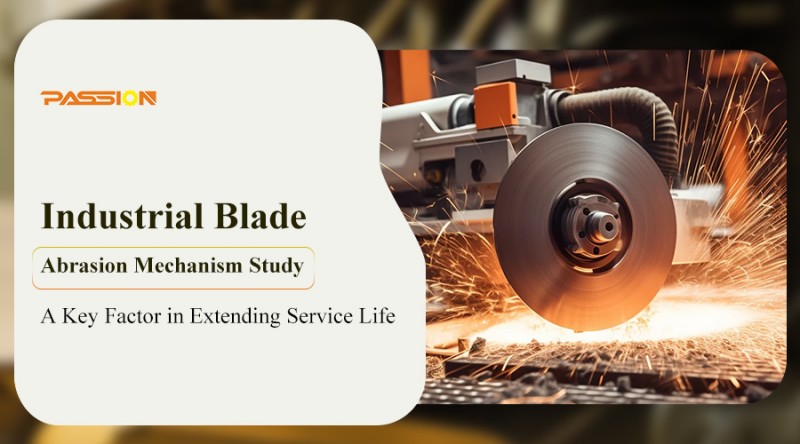
W dziedzinie produkcji przemysłowej ścieranie ostrzy zawsze było ważnym czynnikiem wpływającym na wydajność i jakość produktu. Wraz z postępem nauki i technologii oraz ciągłą optymalizacją procesu, badania nadOstrze przemysłoweMechanizm ścierania staje się coraz bardziej dogłębny, dążąc do znalezienia kluczowych czynników przedłużenia żywotności usług ostrza.

Istnieją różne powody ścierania ostrza, w tym głównie zużycie mechaniczne, zużycie termiczne, zużycie chemiczne i zużycie dyfuzyjne. Mechaniczne ścieranie jest spowodowane głównie twardymi cząsteczkami w materiale obrabianym, aby wytwarzać rowki na powierzchni ostrza, a tego rodzaju ścieranie jest szczególnie oczywiste podczas cięcia przy niskich prędkościach. Ścieranie termiczne wynika z dużej ilości ciepła wytwarzanego podczas procesu cięcia, co powoduje odkształcenie plastikowe ścierania ostrza lub pęknięcia termiczne. Zużycie chemiczne to tlen w powietrzu w wysokich temperaturach i reakcja chemiczna materiału ostrza, tworzenie się związków o niskiej twardości, z dala od chipu, co powoduje ścieranie ostrza. Z drugiej strony ścieranie dyfuzyjne polega na tym, że podczas procesu cięcia elementy chemiczne na powierzchni kontaktowej przedmiotu obrabianego i ścieranie ostrza rozpowszechniają się ze sobą w stanie stałym, zmieniając strukturę składu ostrza i sprawiają, że jego warstwa powierzchniowa krucha.
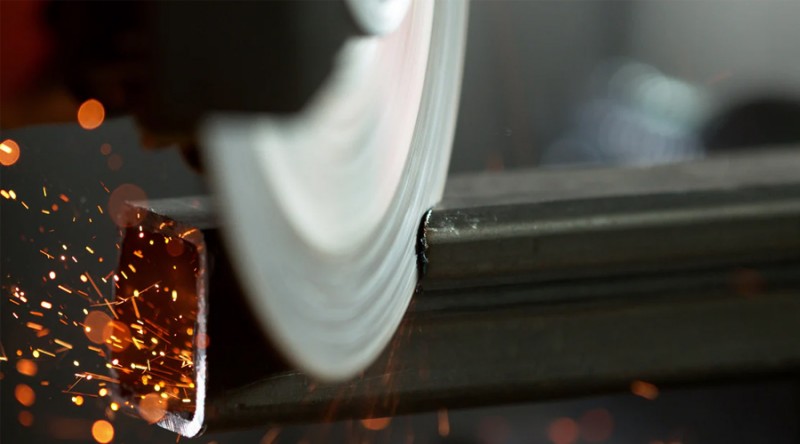
W przypadku tych mechanizmów zużycia naukowcy zaproponowali różnorodne metody przedłużenia żywotności usługi ścierania ostrzy. Przede wszystkim kluczowym jest rozsądny wybór materiałów ostrzy. Zgodnie z charakterystyką przetworzonego materiału i warunków cięcia wybór materiału ostrza z wystarczającą twardością, odpornością na zużycie i wytrzymałość może skutecznie zmniejszyć ścieranie. Na przykład, przy obróbce trudnych do wycięcia materiałów o dużej tendencji do stwardnienia, należy wybrać materiał ostrza o silnej odporności na spawanie zimne i silną odporność na dyfuzję.
Po drugie, optymalizacja parametrów geometrii ostrzy jest również ważnym sposobem przedłużenia żywotności serwisowej. Rozsądny kąt łopatki i kształt ostrza mogą zmniejszyć siłę cięcia i ciepło cięcia oraz zmniejszyć ścieranie ostrzy. Na przykład odpowiednia redukcja przednich i tylnych kątów oraz zastosowanie większej ujemnej nachylenia krawędzi mogą zmniejszyć zużycie krawędzi tnącej. Jednocześnie szlifowanie ujemnego łuku fazowego lub krawędzi może również zwiększyć wytrzymałość końcówki ostrza i zapobiec odpryskiwaniu.
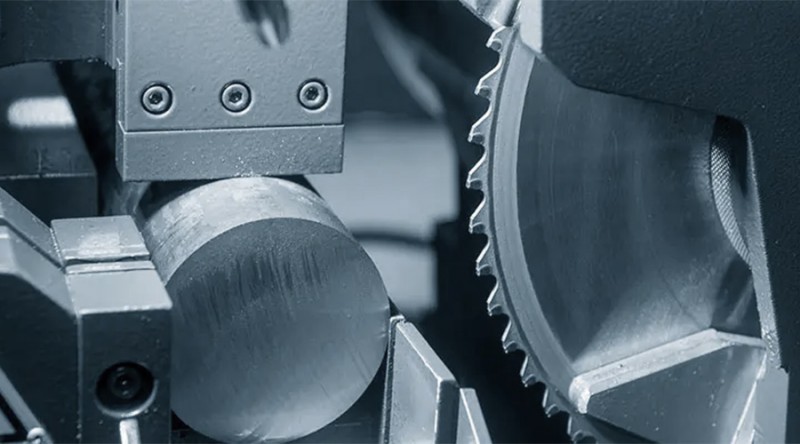
Ponadto rozsądny wybór dawkowania cięcia i zastosowanie smaru chłodzącego jest również skutecznym sposobem przedłużenia żywotności ostrzy. Głębokość cięcia i zasilania jest zbyt duża, siła cięcia wzrasta, a ścieranie ostrza jest przyspieszane. Dlatego, zgodnie z założeniem zapewnienia wydajności przetwarzania, należy zminimalizować ilość cięcia. Jednocześnie stosowanie smarów chłodzących może pochłaniać i usuwać większość ciepła w strefie cięcia, poprawić warunki rozpraszania ciepła, zmniejszyć temperaturę cięcia ostrza i przedmiotu obrabianego, zmniejszając w ten sposób ścieranie ostrza.
Wreszcie, prawidłowa metoda działania i sztywność systemu procesu są również czynnikami, których nie można zignorować. W procesie cięcia ostrze powinno starać się, aby ostrze nie nosi ani mniej nosi nagłą zmianę obciążenia, aby uniknąć ostrza z powodu nierównej siły i pęknięcia. Jednocześnie, aby upewnić się, że system procesowy ma dobrą sztywność, zmniejszenie wibracji może również skutecznie przedłużyć żywotność obsługi ostrza.
Podsumowując, kluczowe czynniki przedłużenia żywotności wkładek przemysłowych obejmują rozsądny wybór materiałów ostrzy, optymalizacja parametrów geometrii ostrzy, rozsądny wybór dawkowania cięcia, zastosowanie smarów chłodzących oraz prawidłowe metody działania i sztywność systemu procesu. Wraz z ciągłym pogłębianiem badań nad mechanizmem ścierania ostrzy uważa się, że w przyszłości pojawią się bardziej innowacyjne technologie i metody, wprowadzając nową witalność do rozwoju branży przemysłowej.
Później będziemy nadal aktualizować informacje, a więcej informacji można znaleźć na naszym blogu witryny (PassionTool.com).
Oczywiście możesz również zwrócić uwagę na nasze oficjalne media społecznościowe:
Czas po: 15.102024